Ever wondered how those powerful farm machines come to life? Let’s take you behind the scenes of a modern tractor factory in India, where raw metal transforms into rugged farming partners!
1. Design & Engineering
- Engineers create 3D digital prototypes, optimizing power, durability, and fuel efficiency.
- Every nut and bolt is virtually tested before production begins.
2. Raw Material Prep
- High-grade steel arrives for the chassis – cut precisely by CNC laser machines.
- Critical parts (engine, gearbox, axles) are sourced from trusted suppliers and undergo X-ray scans for defects.
3. Assembly Line Action
- Chassis Welding: Robotic arms weld the frame with millimeter precision.
- Engine Mounting: The heart of the tractor—4-cylinder diesel engines—are lowered into place.
- Gearbox & Transmission: Heavy-duty components are bolted on using automated torque wrenches.
- Hydraulics & Wiring: A maze of hoses and sensors is installed for attachments like ploughs.
4. Painting & Branding
- The tractor gets a rust-proof electrostatic paint bath (think: durable powder coating).
- Decals and logos are applied—your favorite brand’s signature green, red, or blue!
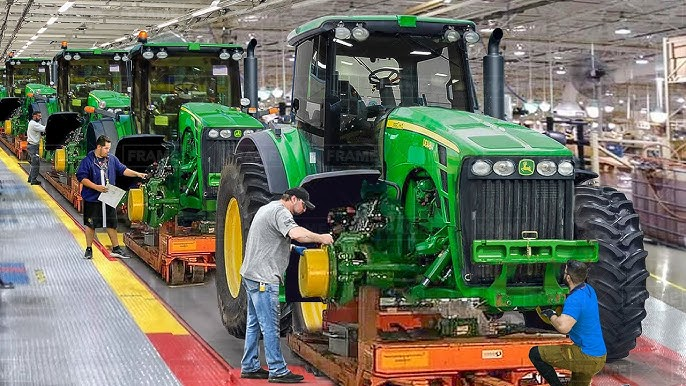
5. Rigorous Testing
- Engine Roar Test: Runs for hours to check performance under load.
- Hydraulic Pressure Check: Ensures lift systems won’t fail mid-field.
- Field Simulation: Tires roll over mock furrows to test suspension.
6. Ready for the Farm!
- After 2–5 days of assembly, the tractor is crated and shipped to dealers.
- Fun Fact: Modern factories use AI cameras to spot even a misaligned bolt!
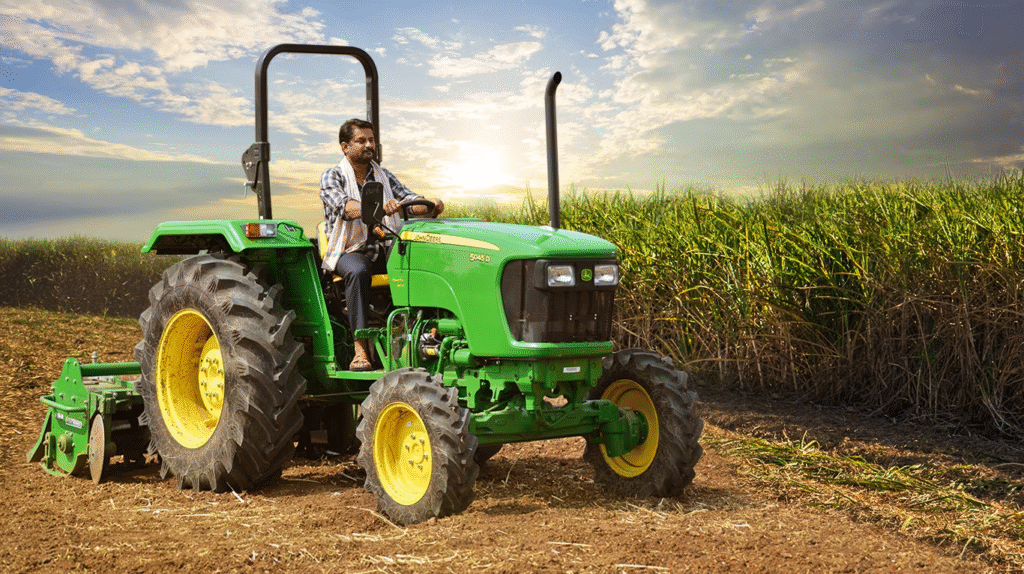
Why It Matters
These machines endure decades of tough work—thanks to robotic welding, CNC precision, and relentless quality checks.
Want to see more factory secrets? Drop a comment! 🚜💨